To make humanitarian operations more sustainable, all actors must use resources smarter: use less and waste less. At Better Shelter, we are actively working through product development to do our part. We are, therefore, particularly excited about this recent project with Konstfack, the University of Arts, Crafts, and Design in Stockholm.
During the autumn, we collaborated with students from Konstfack enrolled in the Design for Sustainable Development module. This course focuses on circular design and social sustainability. It encourages students to examine materials, systems, and products in a new way and learn how to use them in real-life situations.
The students worked on five projects focused on repurposing parts of our shelters into items valuable in camps and disasters.
Ariadne Sandberg Karali, Lukas Eriksson and Axel Åkerblom reused materials from the RHUs to create sustainable and long-lasting solutions for Venezuelan refugees living in UNHCR camps in Boa Vista, Brazil. They ended up developing fan blades of repurposed RHU parts to address extreme heat in the camp.
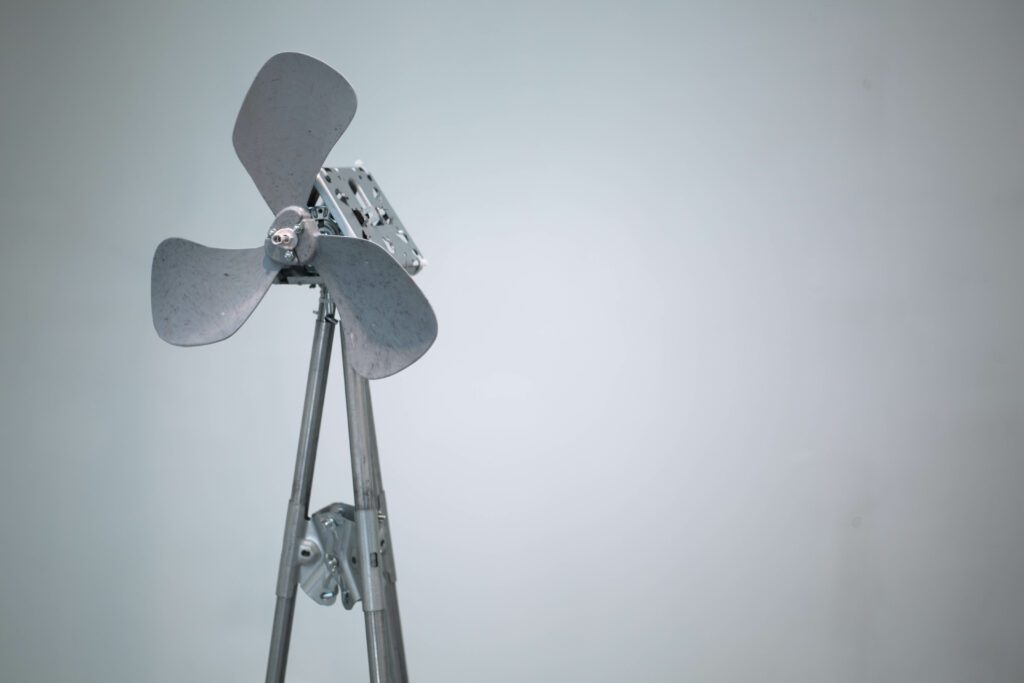
We asked them a few questions:
Tell us about your project!
Boa Vista has consistently high temperatures throughout the year, and families in the camp complain about the heat in the RHUs. While fans are available in the camps, they are imported from the other side of the world and are, therefore, not sustainable. This inspired us to design an open-source fan blade-making system, focusing on upcycling RHU materials. By localising production, the system can reduce climate impact and support local economic growth. The shape of the fan blades is inspired by the macaw, a bird native to Venezuela and Brazil.
Which parts of the shelter did you repurpose, and why?
We experimented with melting all plastic components, including nylon bolts, though we eventually focused on foam panels and RHU windows. Foam panels are particularly interesting due to their faster degradation. Melting these panels proved to be the most challenging, but the fan blades we made from the wall panels turned out to be the most unique and creative-looking. Finally, we made the last set of fan blades using crushed pieces of the RHU’s windows. This process was faster and cleaner, resulting in fan blades with a more polished look. We also reused metal framing from the shelter to create a stable and easy-to-assemble base.
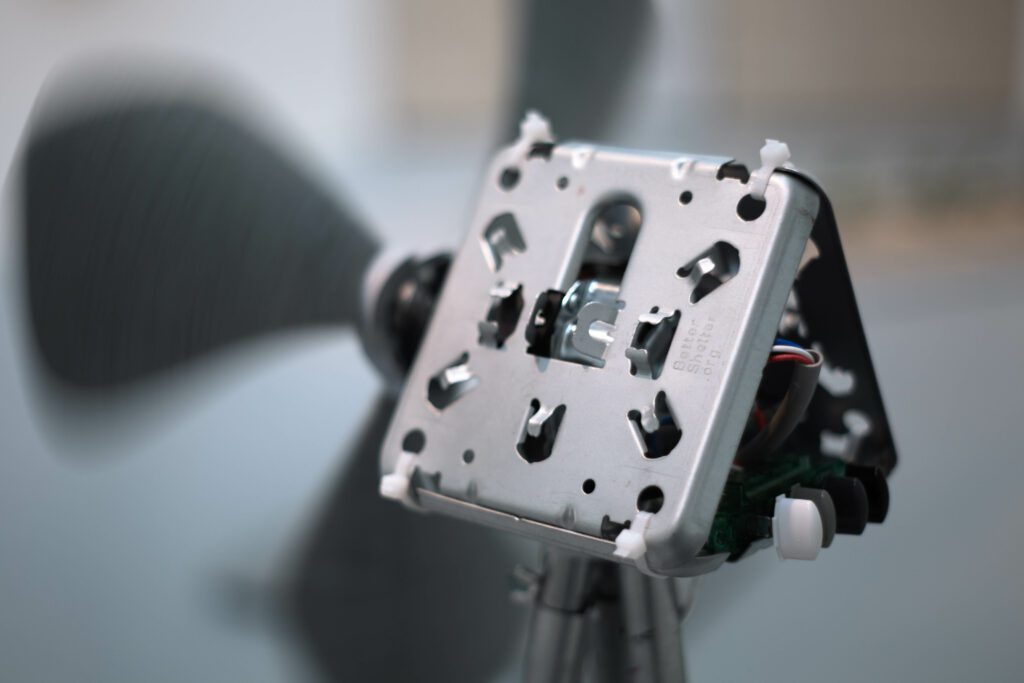
What challenges did you face, and what did you learn from them?
Our biggest challenge was creating a simple plastic production system with minimal components that could still deliver results comparable to those of mass-produced fans. Although an aluminium mould is difficult to produce, it guarantees that the fan blades are balanced. A single gram difference in weight can cause wobbling while spinning.
In what contexts can the recycled fan blades be used?
We decided to showcase the fan blades as part of a standing fan to make it more understandable and easier to visualise, but their potential goes further. We received feedback from the Technical Support Manager at Better Shelter, who suggested integrating them into exhaust systems for RHUs. Also, since plastic waste is a global issue, this system is adaptable beyond Brazil, the concept can be applied anywhere there is plastic waste and a way to melt it, which make it adaptable to various contexts.
Do you have more ideas or suggestions for improvements in the future?
We would love to explore the possibility of making a balanced fan without using the aluminium mould. A simpler system would make the process faster and require fewer resources at the start. As the project grows, we can gradually increase production and complexity.
A glance at the other projects
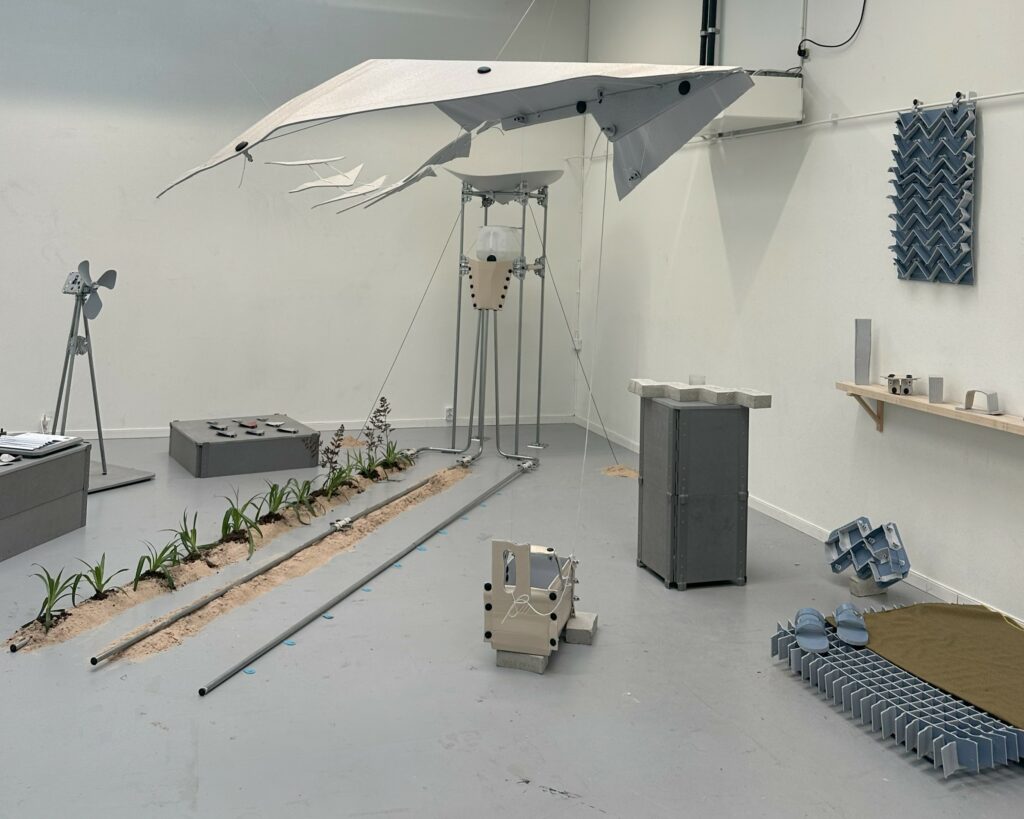
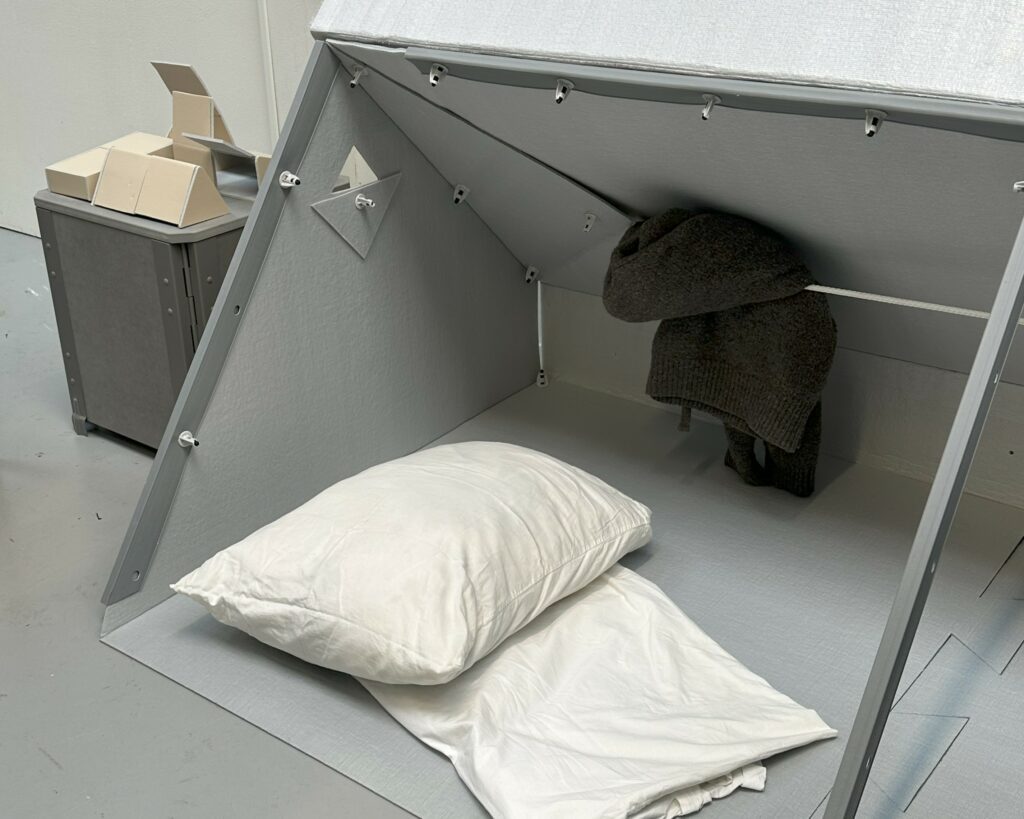
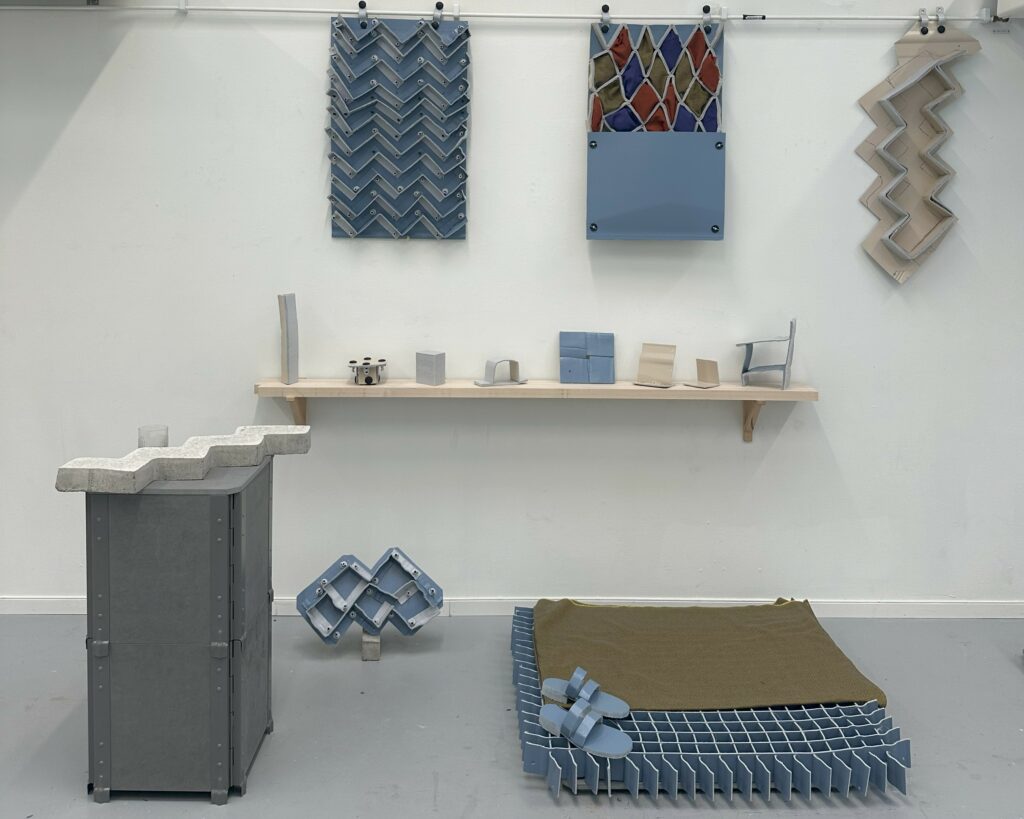
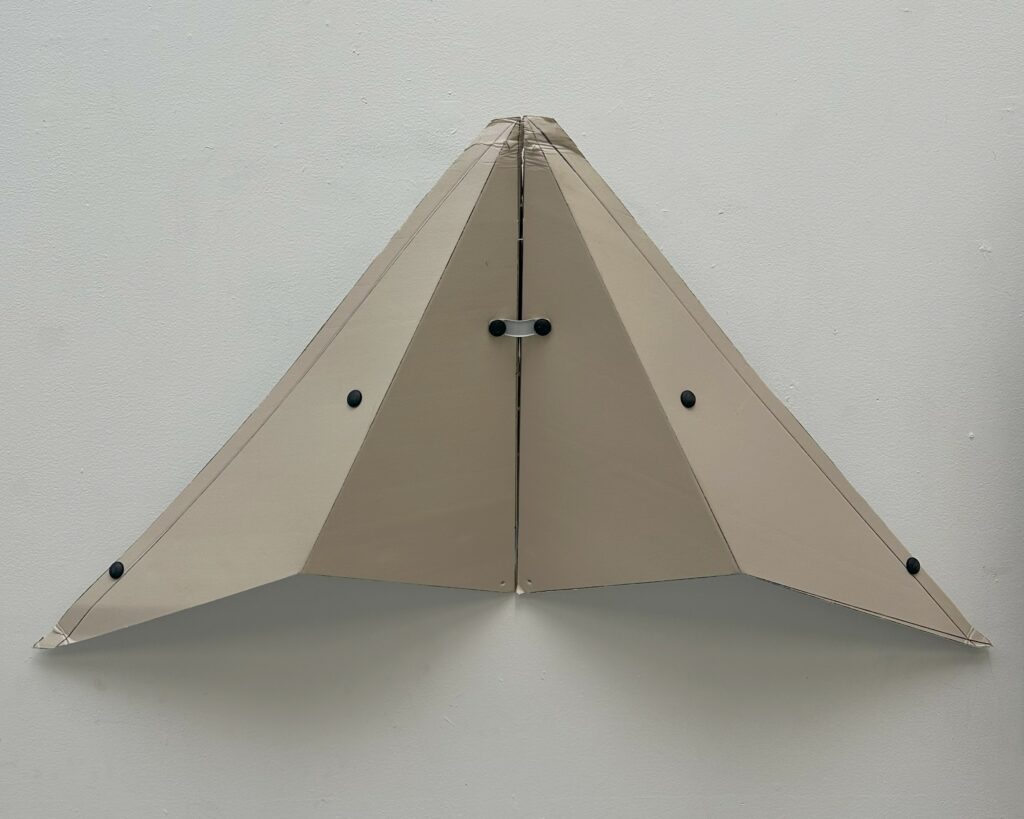
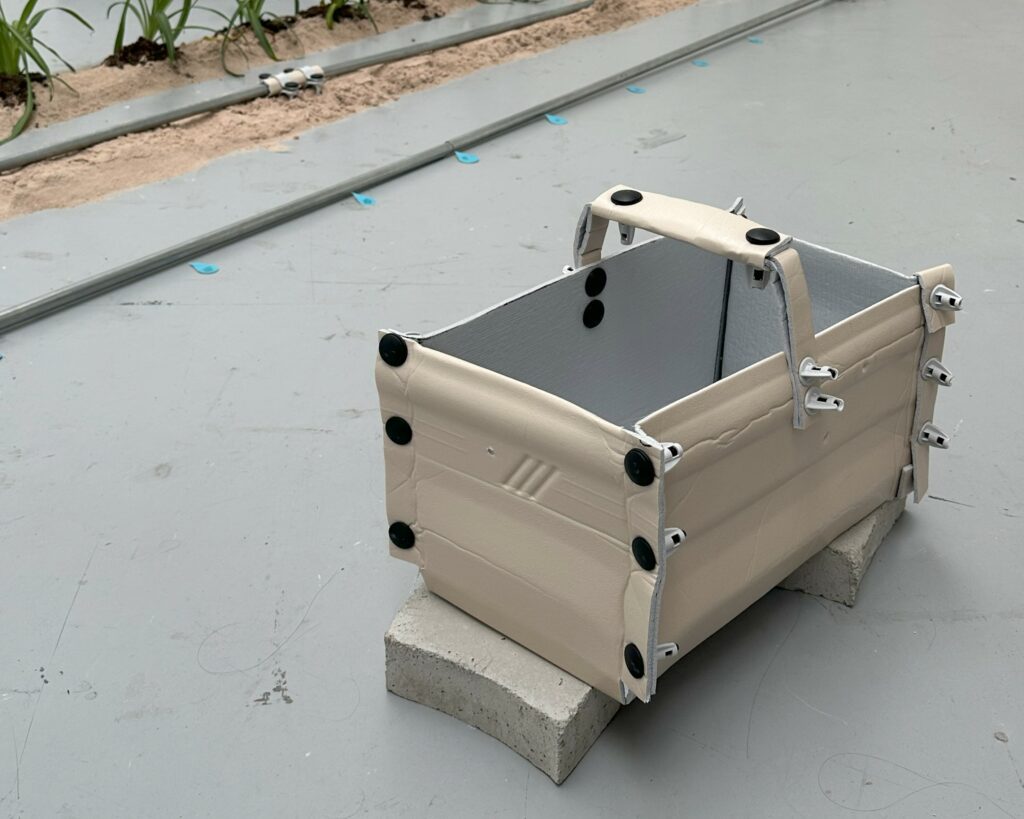
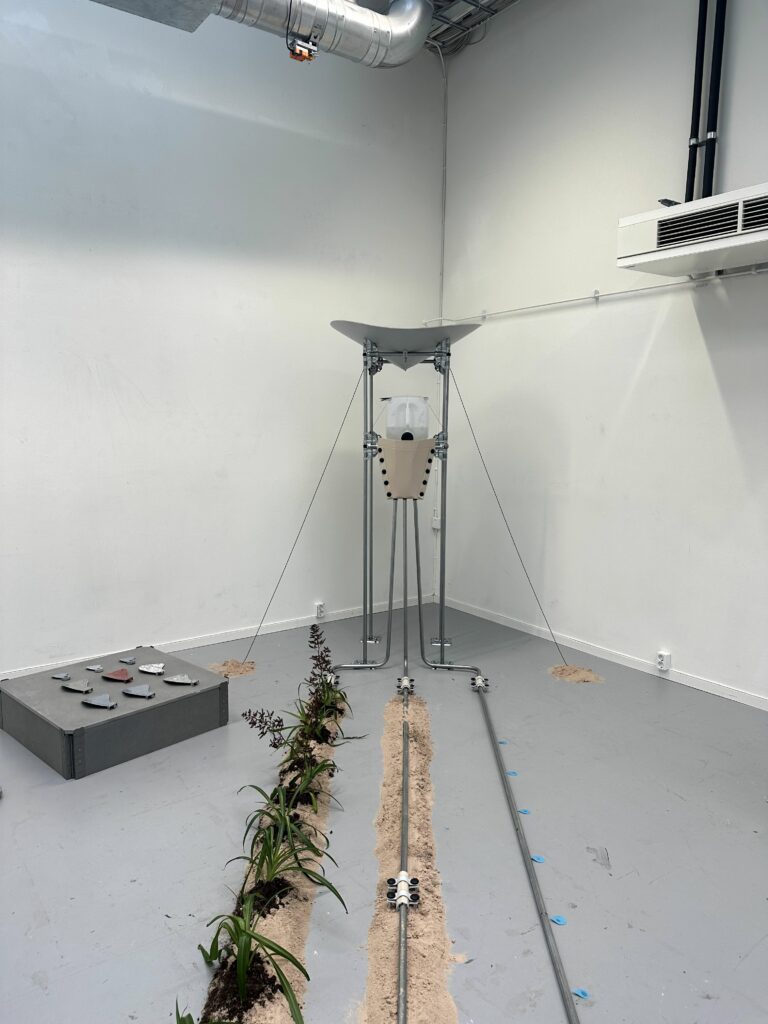